Raytheon Technologies
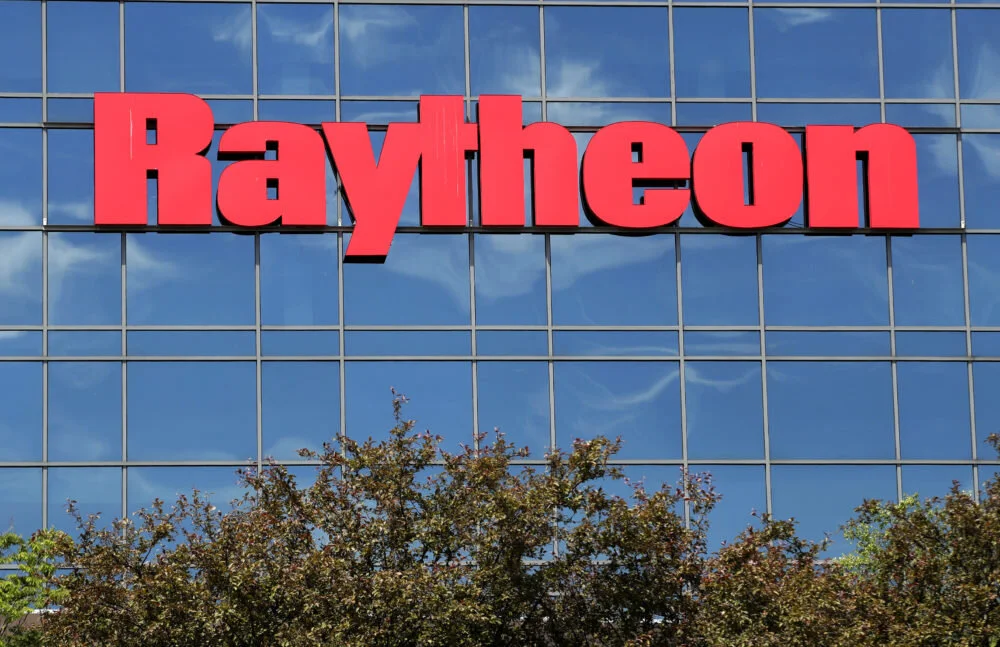
Test Equipment Mechanical Engineer I
At Raytheon Technologies, I am a Mechanical Engineer I for the Test Equipment team. We are responsible for coordinating with a team of electrical engineers to produce equipment that allows field testing of various products that Raytheon manufactures. We use Creo Parametric 5 for 3D design along with drawings of parts and assemblies and AutoCAD for 2D cable drawings.
Personally, I am responsible for the design of test equipment chassis, racks, and various custom parts that allow testing to happen. So far this year, I have designed and overseen production of three full equipment racks. This involved custom design of the overall racks and each individual chassis that is housed in the rack. Custom parts such as brackets, hinges, and adapters were required as well.
Each part and assembly designed goes through a rigorous documentation, checking, and releasing protocol, which requires attention to detail along with constant communication with senior mechanical engineers on my team. Following the release, I contact vendors for quoting and manufacturing and oversee production of my assemblies.
Additionally, I completed a 6sigma project within the first six months of working at Raytheon. A program had been using overpriced cast steel for machinery covers. They were overdesigned and the legacy vendor had not been reconsidered for years. I located this issue from working on related projects, and decided to change it. Through a simple redesign and re-quoting from a new vendor, I managed to lower the cost of a cover from $3000 to just $400. Given that each full assembly used up to 25 of the covers, the cost per assembly greatly outweighed the cost of labor to change the design.
I have signed an NDA at Raytheon, so I am unable to provide pictures of my work completed here